PROCESSING APPLICATION
Hold tight! We’re comparing your resume to the job requirements…
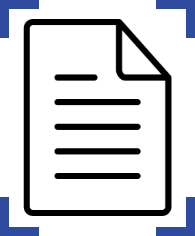
ARE YOU SURE YOU WANT TO APPLY TO THIS JOB?
Based on your Resume, it doesn't look like you meet the requirements from the employer. You can still apply if you think you’re a fit.
Job Requirements of Laboratory Technician 1- R&D Co-op:
-
Employment Type:
Contractor
-
Location:
Exton, PA (Onsite)
Do you meet the requirements for this job?
Laboratory Technician 1- R&D Co-op
Laboratory Technician 1
Duration: 6 Months+ Contract
40hrs/week- FT Contract
Location: Exton, PA
Shift: 1st Shift
Job title: R&D Co-op
Business Unit: Client Biomedical
Department: Innovation/R&D
Position in the organization
Reports to: R&D Group Lead
Direct reports: none
Indirect reports: none
Organization chart: on P & O website
Purpose of the job
Assure that *** Biomedical products are of consistent and high quality by: Assuming responsibility for duties related to the research, development, testing and manufacturing of medical device materials, products or technologies in compliance with GMP and ISO standards and participating on project teams consisting of R&D, Commercialization, Advanced Engineering, Manufacturing, Quality, Regulatory, Business Development and Finance within the PMP/project management process.
Job Context
•** Biomedical is the world’s unrivaled biomaterials expert and committed partner in driving sustainable innovation in healthcare. For more than 30 years, the company has been at the forefront of biomaterial science and process innovation, and the leading resource for global medical device and pharmaceutical companies. As a strategic partner with an approach driven not only by market dynamics but by the unique needs of every customer, *** Biomedical brings an unparalleled breadth of product portfolios, proprietary manufacturing and processing capabilities, world-class IP, and extensive regulatory experience and expertise. Furthermore, *** Biomedical’s products and services are recognized for their unmatched quality, consistency, and performance in multiple markets across the globe, supporting their company-wide vision of solving the world’s healthcare needs through sustainable science. To learn more, visit DSMBiomedical.com.
R&D Context
The R&D activities range from platform R&D (technology and competence development) to product / formulation development R&D (customization of product technology for a specific client/market application; and transformation of platform technology from its fundamental state to commercial realization in (eventual) collaboration with client partners). The key objective for product / formulation development R&D encompasses customization of existing product technology for a specific client/market application and/or the transformation of platform technology from its fundamental state to commercial realization in (eventual) collaboration with client partners. The product / formulation R&D team operates between research (internal and external), business development and external business partners and is required to effectively integrate these different interactions in order to operate successfully. The key objective for platform R&D is proof-of-feasibility / proof-of-concept technology development driven by business needs and technology pipeline strategies. Under platform R&D also the development of new or unmet technology competences (skills and expertise development) is Producted.
The R&D portfolio has a strong multi-disciplinary character, i.e., comprising breadth of science & technology, application fields, and involvement of other disciplines such as Safety & Toxicology, Quality Assurance and Regulatory Affairs, Manufacturing / Operations, Sourcing, and others. Customer and market-driven R&D means providing solutions for unmet clinical needs at large, and customers' technology needs in particular. Important factors of success in Biomedical R&D comprise (i) consistently delivering the greatest level of quality with our products and services, and pursuing continuous improvement of our enabling management systems; (ii) the necessity to complement internal R&D efforts with strategically sourced external R&D and innovation; the latter particularly encompasses effective relationship building and interfacing with academic and clinical institutes, contract research organizations as well as small and large companies; and (iii) ceaselessly striving for enhancement of capabilities and competencies.
Job Content
This role involves designing and executing experiments, analyzing results, and staying abreast of emerging trends in biomaterial research. Additionally, this role will be responsible for developing Client biomaterials, collaborating with cross-functional teams, and ensuring the successful translation of research findings into scalable, market-ready solutions. The individual should demonstrate strong problem-solving skills, a deep understanding of biomaterials, and a passion for advancing biomedical technologies.
Key Areas of Accountability / Responsibility
1. Generate and process Device Master Record documentation, including process routers, drawings, preventative maintenance procedures, and other written documentation in accordance with GMP requirements to support product development, process development, validations, and manufacturing. Prepare relevant technical sections for product or regulatory submissions.
2. Identify, evaluate, and implement improvements (productivity, efficiency, reliability) to existing processes or products. Assist production and quality personnel in the training, initial launch, and validation of new products and processes. Provide technical interface for internal and external stakeholders and customers.
3. Plan, construct, and implement Design of Experiments (DOEs) and Risk Management Documentation as required to develop or validate new or existing products. Develop testing methods and complete Test Method Validation (TMV). Prepare protocols and reports, and provide recommendations based on completed experiments and/or tests. Develop and maintain design control systems and procedures that comply with all US/OUS medical device regulations.
4. Perform analytical, mechanical, and biochemical assay testing, as well as polymer synthesis, polymer processing, natural materials manufacturing and characterization, according to Client Quality Systems protocols for raw materials, intermediates, and finished products while maintaining a laboratory notebook and other associated documents. Independently plans, prioritizes, and conducts research.
5. Complete other tasks as assigned.
SHE & Security
1. It is the responsibility of each employee to work in a safe and responsible manner in order to create an injury-free and incident-free workplace.
2. Complies with all job-related safety, security and other training requirements.
3. Report any SHE and Security incidents (including observed risks) to management.
4. Comply with Client Life Saving Rules.
6. Dimensions for security reasons, not filled in
Dimensions Realization previous year Budget this year Impact Net Sales Value
Contribution Margin
Purchase Value
Added Production Value
Total cost of employment
Departmental or Project Budget
Knowledge and educational level
• Ph.D., Master's, or Bachelor's degree in analytical chemistry, chemistry or polymer science (Analytical Group).
• Skilled in polymer physical and chemical processing techniques, encompassing polymer synthesis, melt processing (extrusion, injection molding, compression molding), solution processing (film casting), foaming, machining, and sterilization.
Experienced in employing analytical techniques such as DSC, TGA, TMA, Rheology, FTIR, GPC, HPLC, as well as mechanical tests including tensile, flexural, torque, torsion, and more for comprehensive polymer characterization (TPU & Polymer Processing Group); Experienced with and/or skilled in materials processing, including physical and chemical processing such as milling, mixing, lyophilization, acid/base reactions, crosslinking, thermal treatment, and sterilization.
Experienced with characterization and analysis of materials using techniques such as mechanical testing, DSC, FTIR, SEM, SDS-PAGE, particle size, surface area, porosity, and more for comprehensive material characterization (Natural Material Group);
Highly skilled in two or more analytical techniques.
Broadly experienced in other analytical techniques.
Experienced with analytical method development, validation and implementation. Demonstrated skill in analytical instrumentation trouble shooting and repair.
Understanding of polymer and natural materials science (Analytical Group).
• Knowledge and experience working with Engineering & Quality tools (Statistics, Six Sigma, DFM, DOE, etc.)
• Computer literacy (i.e. Word, Excel, Project, PowerPoint, Outlook, Pro/E or similar CAD system).
• Understanding of Engineering concepts.
• Understanding of anatomy and surgical procedures.
• Good written and oral communications skills.
• Ability to function or lead as a part of a team.