US
0 suggestions are available, use up and down arrow to navigate them
PROCESSING APPLICATION
Hold tight! We’re comparing your resume to the job requirements…
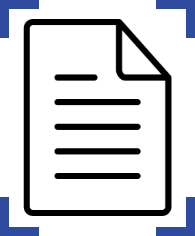
ARE YOU SURE YOU WANT TO APPLY TO THIS JOB?
Based on your Resume, it doesn't look like you meet the requirements from the employer. You can still apply if you think you’re a fit.
Job Requirements of Maintenance/Engineering Tech III:
-
Employment Type:
Contractor
-
Location:
Boulder, CO (Onsite)
Do you meet the requirements for this job?
Maintenance/Engineering Tech III
Careers Integrated Resources Inc
Boulder, CO (Onsite)
Contractor
TITLE: Maintenance tech/Engineering tech
Purpose
The Sr. Maintenance Technician is responsible for ensuring all site facilities, Utilities and equipment are maintained in an operational and calibrated state. This includes ensuring all necessary documentation is tracked and organized, on-time execution of required maintenance, timely response to repairs in order to maintain both production and development processes within the site.
ESSENTIAL FUNCTIONS
•Hands on- ability to troubleshoot and repair electrical, HVAC and general maintenance
Lead maintenance activities for equipment in use at the site; coordinate, plan and deliver to schedule, ensuring compliance with local procedures and adherence to corporate policies.
Facilitate and organize maintenance work for onsite equipment to ensure performance of equipment and instrumentation to be used in GMP operations.
Create, track, and organize documentation for maintenance activities.
Coordinate and interact with suppliers/vendors for work and materials as it pertains to support activities within the facility.
Work with management team in establishing internal maintenance programs.
Track, update, and support continuous monitoring system (manage sensor replacements for maintenance, and repair activities).
Review supplier documentation to ensure it meets *** quality standards and conforms to local guidance.
Installation, setup and support for qualification activities as-needed for new equipment and scale-up/build-out of the plant.
Perform periodic inspections of facilities and systems (Assist with periodic review and reporting of facility systems as-needed).
Organize and maintain utilities for the site.
Provide input and recommendations on cost-saving opportunities.
Perform projects individually or as part of a team.
Support activities in other departments as requested.
PHYSICAL REQUIREMENTS
Physical Requirements 20-30% overnight travel required; Ability to work flexible hours and overtime.
QUALIFICATIONS
Minimum HS Diploma required, Associate degree or technical certification preferred. Advanced degree may be substituted for experience as appropriate. Licensure (electrical, HVAC,Jorneyman) is a plus.
5+ years of experience in a regulated cGMP environment highly preferred. Prior experience working in a life science company as a facilities engineering technician or engineering technician highly preferred
3+ years of experience in organizing, maintaining, and documenting maintenance programs is required.
3+ years of experience with equipment maintenance and systems is required.
HVAC experience is a plus
-Inventory management
Experience using a Client and/or CMMS in a life science company
Experience maintaining diagnosing and repairing industrial equipment and lab equipment, such as changing seals, pumps, valves, fittings, pressure regulators, and hoses.
Understanding standard lab equipment is strongly preferred (incubators, centrifuges, HPLC, Mass Spec).
Experience overseeing, calling, and managing site vendors such as HVAC vendors, process equipment vendors (Cytiva, Agilent ), electrical vendors, and plumbing vendors.
Experience interacting with R&D, quality, validation, manufacturing. Able to communicate well across all levels to explain the support provided with various projects.
Experience with GDP (especially for calibration and maintenance) is highly preferred.
Strong organizational, troubleshooting, communication and interpersonal skills are essential.
Ability to work on fast-paced, collaborative teams and demonstrate flexibility in response to changing priorities is a must.
Ability and desire to support the team with additional tasks as needed.
Purpose
The Sr. Maintenance Technician is responsible for ensuring all site facilities, Utilities and equipment are maintained in an operational and calibrated state. This includes ensuring all necessary documentation is tracked and organized, on-time execution of required maintenance, timely response to repairs in order to maintain both production and development processes within the site.
ESSENTIAL FUNCTIONS
•Hands on- ability to troubleshoot and repair electrical, HVAC and general maintenance
Lead maintenance activities for equipment in use at the site; coordinate, plan and deliver to schedule, ensuring compliance with local procedures and adherence to corporate policies.
Facilitate and organize maintenance work for onsite equipment to ensure performance of equipment and instrumentation to be used in GMP operations.
Create, track, and organize documentation for maintenance activities.
Coordinate and interact with suppliers/vendors for work and materials as it pertains to support activities within the facility.
Work with management team in establishing internal maintenance programs.
Track, update, and support continuous monitoring system (manage sensor replacements for maintenance, and repair activities).
Review supplier documentation to ensure it meets *** quality standards and conforms to local guidance.
Installation, setup and support for qualification activities as-needed for new equipment and scale-up/build-out of the plant.
Perform periodic inspections of facilities and systems (Assist with periodic review and reporting of facility systems as-needed).
Organize and maintain utilities for the site.
Provide input and recommendations on cost-saving opportunities.
Perform projects individually or as part of a team.
Support activities in other departments as requested.
PHYSICAL REQUIREMENTS
Physical Requirements 20-30% overnight travel required; Ability to work flexible hours and overtime.
QUALIFICATIONS
Minimum HS Diploma required, Associate degree or technical certification preferred. Advanced degree may be substituted for experience as appropriate. Licensure (electrical, HVAC,Jorneyman) is a plus.
5+ years of experience in a regulated cGMP environment highly preferred. Prior experience working in a life science company as a facilities engineering technician or engineering technician highly preferred
3+ years of experience in organizing, maintaining, and documenting maintenance programs is required.
3+ years of experience with equipment maintenance and systems is required.
HVAC experience is a plus
-Inventory management
Experience using a Client and/or CMMS in a life science company
Experience maintaining diagnosing and repairing industrial equipment and lab equipment, such as changing seals, pumps, valves, fittings, pressure regulators, and hoses.
Understanding standard lab equipment is strongly preferred (incubators, centrifuges, HPLC, Mass Spec).
Experience overseeing, calling, and managing site vendors such as HVAC vendors, process equipment vendors (Cytiva, Agilent ), electrical vendors, and plumbing vendors.
Experience interacting with R&D, quality, validation, manufacturing. Able to communicate well across all levels to explain the support provided with various projects.
Experience with GDP (especially for calibration and maintenance) is highly preferred.
Strong organizational, troubleshooting, communication and interpersonal skills are essential.
Ability to work on fast-paced, collaborative teams and demonstrate flexibility in response to changing priorities is a must.
Ability and desire to support the team with additional tasks as needed.
Get job alerts by email.
Sign up now!
Join Our Talent Network!